Quality Inspection for Metal Roll Forming Companies - sandwich panel production line – Xinnuo Detail:
*Detail
Sandwich panel production line is especially designed for producing insulation composite board. With stepless speed regulation system, It Is able to produce corrugated composite panel efficiently at one time. Sandwich panel roll forming machine has been an indispensable device in fabricating roof panels and wall panels in plants and warehouses, among other buildings.
*Features
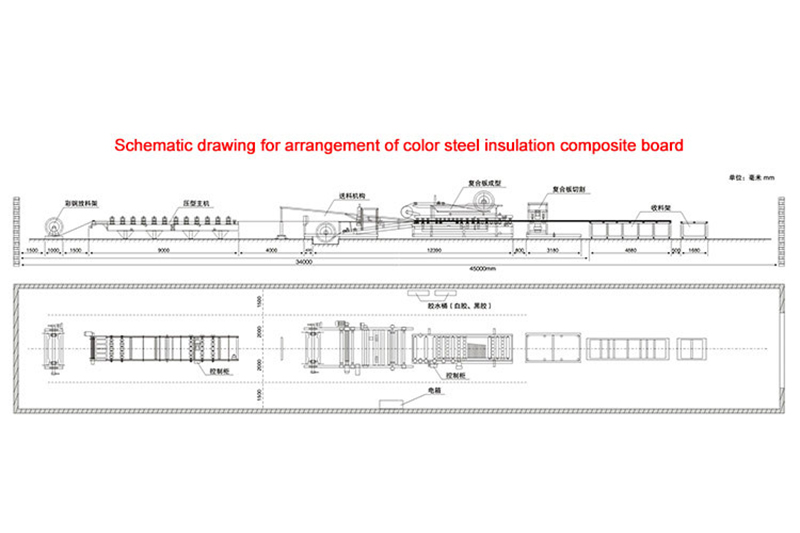
*Features
1. The motor power of the sandwich panel roll forming line is 4k and the production speed reaches 6mmln. With the stepless speed regulation system, the efficiency of the roll forming line is optional within O-6m mm.
2. ben producing EPS sandwich panel, the speed is generally controlled at 2-6 m mm. It will be slightly lower for making rock wool board (depends on actual needs)
3. The composite panel production line Is equipped with K.9 glue metering pump, featuring low rotating speed and high accuract The glue is fed at a rate of 0.1-2.0 kg mm. It is controlled by frequency converter.
4. The thickness of the composite panel the roll forming unit can produce is varied from 50mm to 0mm. By adjusting the upper and lower rack, and the distance between the cutter holder and the material feeding rack, we can get sandwich boards with different thickness and specifications.
5. Total installed capacity: 34KW”; total weight (including accessories): 17.5t.
6. Dimension of the panel roll forming machine: 12500 (16000 for rock wool boards) X2200X2800; the roll former for 5 type EPS sandwich panel adopts 23 rubber shafts and 160X80 square tubes with thickness of 6mm; the roll former for 7 type composite rock wool panel employs 43 rubber shafts, and upper and lower independent glue suppb It is equipped with 1. 7m rock wool panel conveyor belt, with the diameter of the drive shaft to be 30mm; length of the machine frame Is up to Qm; the roll former Is welded with 180X80 square tubes which thickness Is 8mm.
*Requirements for Factories
The factories where our metal deck roll forming machines are applied can be either flat-roof or sloped-roof type. The height of the cornice should be larger than 3m, and the effective width should be at least 45m. The floor of the factory should be flat and concrete. For foundation of the roll forming line, it is required to be designed according to the drawings and fmished before the equipment arrives. The power supply is required to be 380 and the total installed power Is 34kw. It Is necessary for the facto to be equipped with 0.4-0.6MPa compressed air supply and illumination devices. The roll forming machine shares the same power supply with the auxiliary devices. The fluctuation of voltage should be no more than l0%, or it may lead to an abnormal running of the system.
The stroke is no less than 29m, the load for a lifting process is larger than 5000kg, and the lifting height Is no less than 3.Qm. For daily production and maintenance, about 8.10 people are needed, with 3.4 operators for some core processes included.
*Application
Sealing side device for rockwool panel
cutting system
Four rubber pumps are controlled by two motors
Thick rubber shaft
Electric folding device
roll forming machine
control system
Extended conveyor belt
*Deliver goods
Product detail pictures:
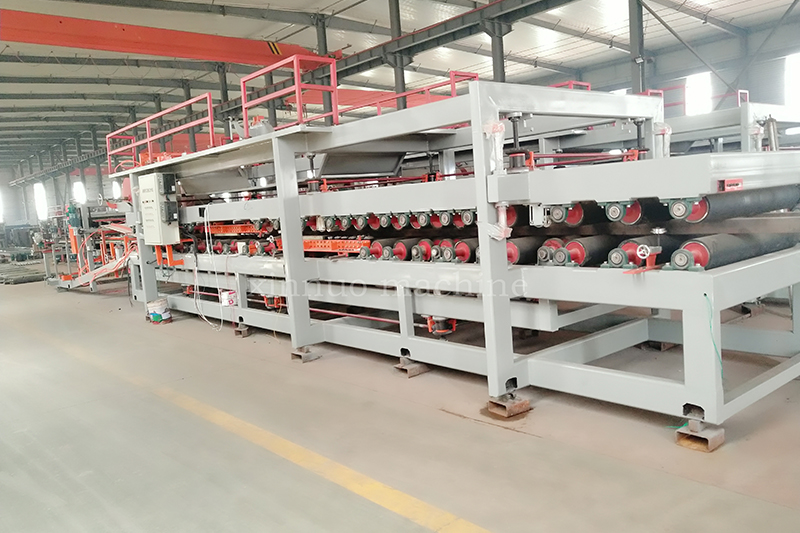
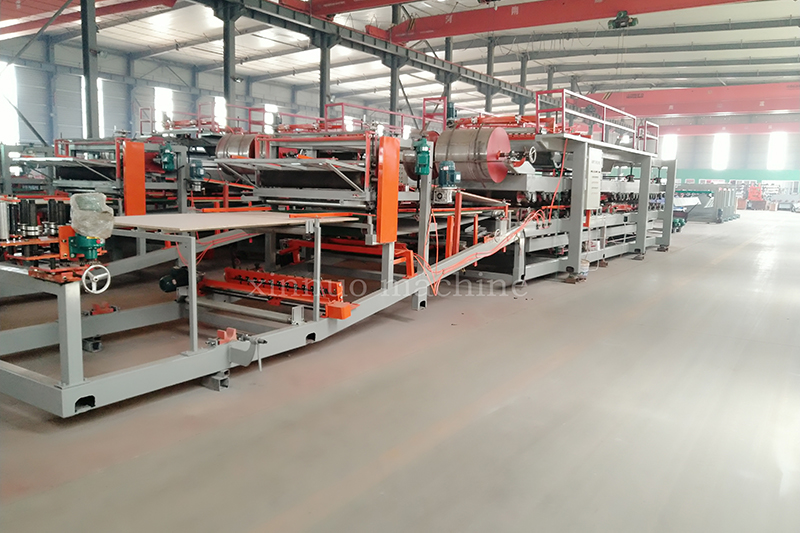
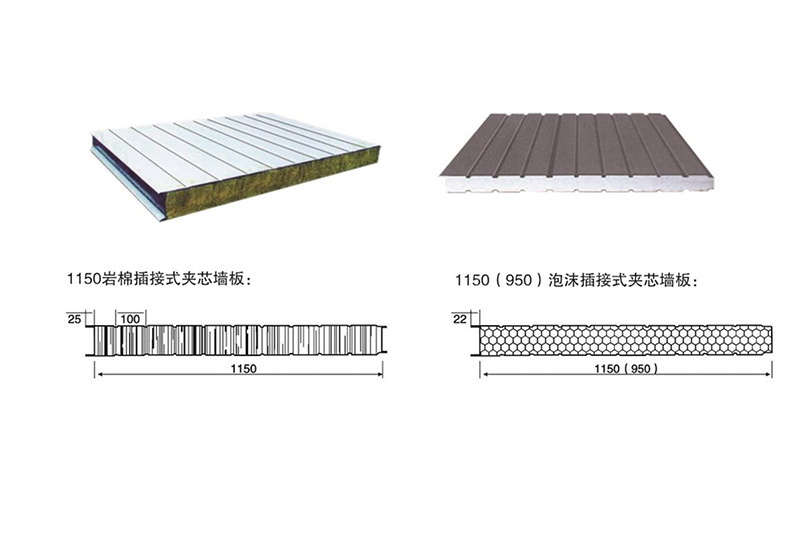
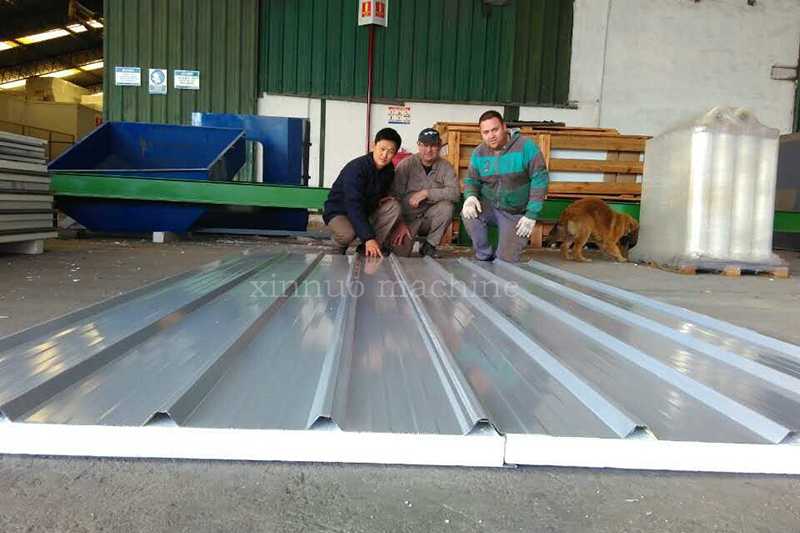
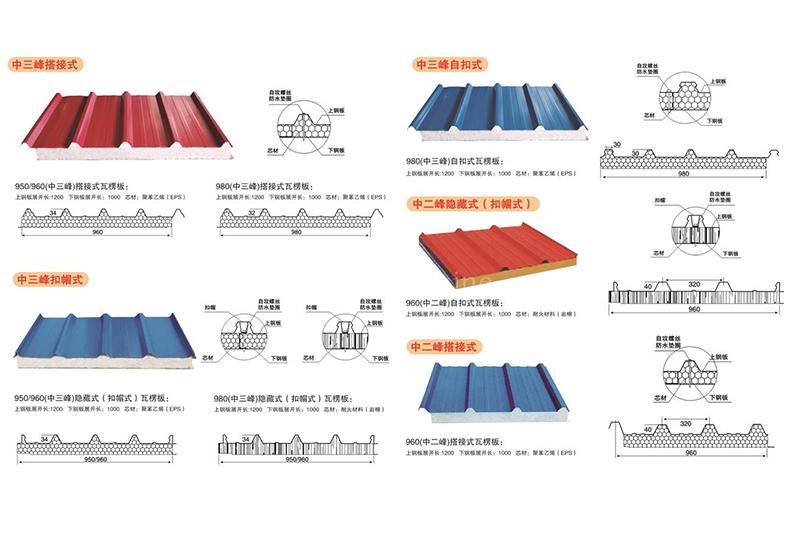
Related Product Guide:
With advanced technologies and facilities, strict high-quality handle, reasonable rate, superior services and close co-operation with prospects, we are devoted to furnishing the best price for our customers for Quality Inspection for Metal Roll Forming Companies - sandwich panel production line – Xinnuo, The product will supply to all over the world, such as: Italy , Swedish , United States , We adopt advanced production equipment and technology, and perfect testing equipment and methods to ensure our product quality. With our high-level talents, scientific management, excellent teams, and attentive service, our products are favored by domestic and foreign customers. With your support, we will build a better tomorrow!
♦ COMPANY PROFILE:
Hebei Xinnuo Roll Forming Machine Co., Ltd., not only produce different types of professional roll forming machines, but also develop intelligent automatic roll forming production lines, C&Z shape purline machines, highway guardrail roll forming machine lines, sandwich panel production lines, decking forming machines, light keel machines, shutter slat door forming machines, downpipe machines, gutter machines, etc.
Advantages of Roll Forming A Metal Part
There are several advantages of using roll forming for your projects:
- The roll forming process allows operations such as punching, notching, and welding to be performed in-line. Labor cost and time for secondary operations are reduced or eliminated, reducing part costs.
- Roll form tooling allows for a high degree of flexibility. A single set of roll form tools will make almost any length of the same cross-section. Multiple sets of tools for varying length parts are not required.
- It can provide better dimensional control than other competing metal forming processes.
- Repeatability is inherent in the process, allowing easier assembly of roll formed parts into your finished product, and minimizing problems due to “standard” tolerance build up.
- Roll forming is typically a higher speed process.
- Roll forming offers customers a superior surface finish. This makes roll forming an excellent option for decorative stainless steel parts or for parts requiring a finish such as anodizing or powder coating. Also, texture or pattern can be rolled into the surface during forming.
- Roll forming utilizes material more efficiently than other competing processes.
- Roll formed shapes can be developed with thinner walls than competing processes
Roll forming is a continuous process which converts sheet metal into an engineered shape using consecutive sets of mated rolls, each of which makes only incremental changes in the form. The sum of these small changes in form is a complex profile.

Customer service staff and sales man are very patience and they all good at English, product's arrival is also very timely, a good supplier.

-
China Rolling Shutter Patti Machine Factory - ...
-
PriceList for C Channel Roll Forming Machine - ...
-
Wholesale Roof Roll Forming Machine Factory - ...
-
Professional Design Purlin Forming Machine - l...
-
High definition Steel Coil Slitting Line - Hyd...
-
Factory wholesale Hydraulic Forming Machine - ...