Quality Inspection for Metal Roll Forming Companies - wall panel roll forming machine – Xinnuo Detail:
*Detail
Wall panel roll forming machine is generally used for producing wall panels of plants, warehouses, garage, hangar, stadium, exhibition hail, and theaters, etc. It is mainly consisted of material feeding, roll forming, and shearing parts. The PLC computer control and hydraulic pumping systems allow the panel roll forming machine to be rather easy operated and highly automatic. Our design team consisted of over 10 people is committed to customizing roll forming machines with various functions for customers.
The wall sheet forming machine is equipped with double-line chain, the pressure of which is distributed evenly at each point of the chain. Its cutting bade is made from Cr12 molybdenum-vanadium steel, featuring high hardness and high wear resistance. Upon clients’ request, we can develop multi language control system for the roll forming machine. Wall panels made by this equipment are of smooth surface and uniform appearance.
*specifiction
Configurations | Manual Uncoiler ,Guiding Platform ,Coil Strip Leveler ,Main Machine Of Roll Forming ,Electro-Motor,Cutting Device ,Hydraulic Station ,PLC Control, Supporter Table. |
Control System | PLC Delta Inverter |
Main Frame | 200-300mm H-Beam |
Main Power | 3-4 kw |
Pump Power | 3 kw |
Power Supply | 380V, 3-Phase,50Hz |
Forming Speed | 15-20m/min |
Cutting speed | 8-12m/min |
Roll Station | 9-13 stands |
Roller Diameter | 70-80mm |
Hydraulic Pressure | 10-12MPa |
Feeding Thickness | 0.3-0.8mm |
Feeding Width | 914mm-1250mm |
Backboard Thickness | 12-16mm |
Chain Size | 20mm |
Cutter Standard | Cr12 |
Roller Standard | 45# |
Cr-Plating Size | 0.05mm |
Overall Size | According to the product |
Total Weight | According to the product |
Product detail pictures:
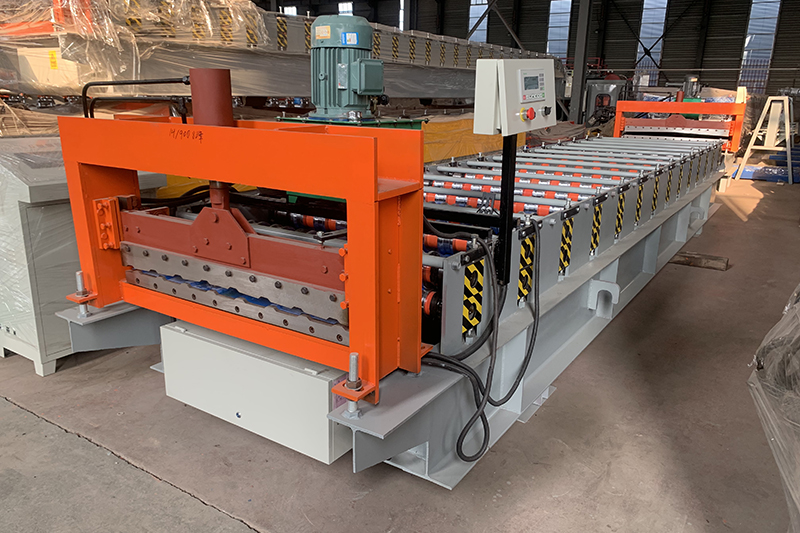
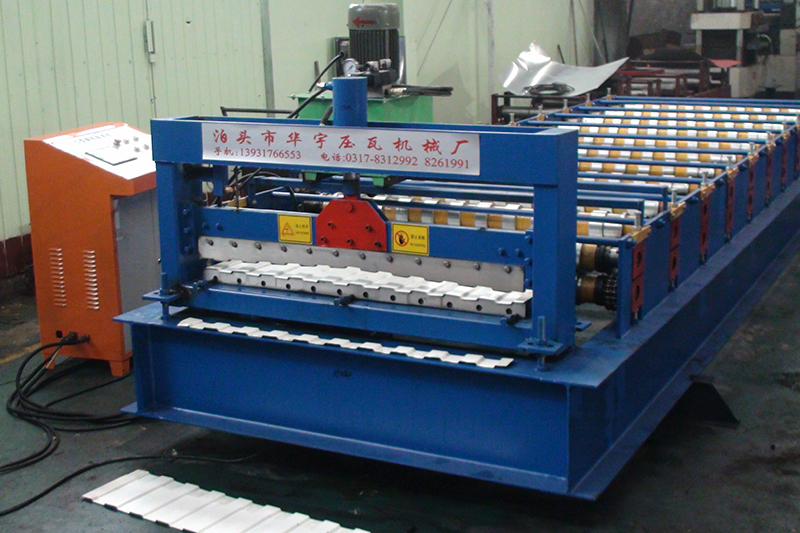
Related Product Guide:
Adhering to the principle of "quality, service, efficiency and growth", we have gained trusts and praises from domestic and international client for Quality Inspection for Metal Roll Forming Companies - wall panel roll forming machine – Xinnuo, The product will supply to all over the world, such as: Naples , Johannesburg , Iran , Customer's satisfaction is always our quest, creating value for customers is always our duty, a long term mutual-beneficial business relationship is what we are doing for. We are an absolutely reliable partner for yourself in China. Of course, other services, like consulting, can be offered too.
♦ COMPANY PROFILE:
Hebei Xinnuo Roll Forming Machine Co., Ltd., not only produce different types of professional roll forming machines, but also develop intelligent automatic roll forming production lines, C&Z shape purline machines, highway guardrail roll forming machine lines, sandwich panel production lines, decking forming machines, light keel machines, shutter slat door forming machines, downpipe machines, gutter machines, etc.
Advantages of Roll Forming A Metal Part
There are several advantages of using roll forming for your projects:
- The roll forming process allows operations such as punching, notching, and welding to be performed in-line. Labor cost and time for secondary operations are reduced or eliminated, reducing part costs.
- Roll form tooling allows for a high degree of flexibility. A single set of roll form tools will make almost any length of the same cross-section. Multiple sets of tools for varying length parts are not required.
- It can provide better dimensional control than other competing metal forming processes.
- Repeatability is inherent in the process, allowing easier assembly of roll formed parts into your finished product, and minimizing problems due to “standard” tolerance build up.
- Roll forming is typically a higher speed process.
- Roll forming offers customers a superior surface finish. This makes roll forming an excellent option for decorative stainless steel parts or for parts requiring a finish such as anodizing or powder coating. Also, texture or pattern can be rolled into the surface during forming.
- Roll forming utilizes material more efficiently than other competing processes.
- Roll formed shapes can be developed with thinner walls than competing processes
Roll forming is a continuous process which converts sheet metal into an engineered shape using consecutive sets of mated rolls, each of which makes only incremental changes in the form. The sum of these small changes in form is a complex profile.

The sales person is professional and responsible, warm and polite, we had a pleasant conversation and no language barriers on communication.

-
Roll Forming Machine Price List - rain gutter ...
-
Oem Shutter Door Roll Forming Machine Manufactu...
-
oem Automatic Roll Forming Machine Manufacturer...
-
high quality Sheet Metal Roll Forming Manufactu...
-
china Roll Forming Equipment factories - sandw...
-
Wholesale Interlocking Tiles Making Machine Quo...