Roof Panel Roll Forming Machine Manufacturers - Sandwich Panel Production Line – Xinnuo Detail:
Sandwich Panel Production Line
1. The overall demensio: 35000mm*2500mm*2600mm
2. Working voltage: 380V
3. The whole power: about 30kw
4. Total weight:25T
5. Working speed: 2-4.5m/min
6. Suitable thickness:0.3-0.8mm
7. Coil thickness:20-300mm
8. Coil material: EPS, rock wool, glass silk floss
Main Characteristics:
1. Factory direct supply price.
2. We have exported for more than 10 years.
3.The frame is produced bu the large CNC machining center for one time, weling with steel plate, processing with
amealing, ensures the high strength, high precision and longer life.
4. The manufacturing process of the complete machine is in strict accordance with the mechanical standards, tracking
and controlling the manufacture of each part. Besides the advanced lubrication system, the working shaft is supported by the heavy bearing, the service life is much longer.
5.The entire line is controlled with PLC, with touch screen of display and operation and high automation.
Packing Details:
Product detail pictures:
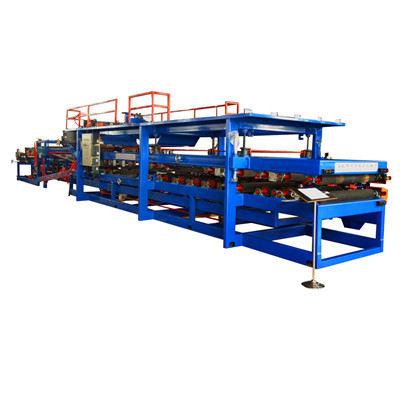
Related Product Guide:
We normally follow the basic principle "Quality Initial, Prestige Supreme". We've been fully committed to offering our consumers with competitively priced good quality merchandise, prompt delivery and professional support for Roof Panel Roll Forming Machine Manufacturers - Sandwich Panel Production Line – Xinnuo, The product will supply to all over the world, such as: Iran , St. Petersburg , Italy , We adopted technique and quality system management, based on "customer orientated, reputation first, mutual benefit, develop with joint efforts", welcome friends to communicate and cooperate from all over the world.
♦ COMPANY PROFILE:
Hebei Xinnuo Roll Forming Machine Co., Ltd., not only produce different types of professional roll forming machines, but also develop intelligent automatic roll forming production lines, C&Z shape purline machines, highway guardrail roll forming machine lines, sandwich panel production lines, decking forming machines, light keel machines, shutter slat door forming machines, downpipe machines, gutter machines, etc.
Advantages of Roll Forming A Metal Part
There are several advantages of using roll forming for your projects:
- The roll forming process allows operations such as punching, notching, and welding to be performed in-line. Labor cost and time for secondary operations are reduced or eliminated, reducing part costs.
- Roll form tooling allows for a high degree of flexibility. A single set of roll form tools will make almost any length of the same cross-section. Multiple sets of tools for varying length parts are not required.
- It can provide better dimensional control than other competing metal forming processes.
- Repeatability is inherent in the process, allowing easier assembly of roll formed parts into your finished product, and minimizing problems due to “standard” tolerance build up.
- Roll forming is typically a higher speed process.
- Roll forming offers customers a superior surface finish. This makes roll forming an excellent option for decorative stainless steel parts or for parts requiring a finish such as anodizing or powder coating. Also, texture or pattern can be rolled into the surface during forming.
- Roll forming utilizes material more efficiently than other competing processes.
- Roll formed shapes can be developed with thinner walls than competing processes
Roll forming is a continuous process which converts sheet metal into an engineered shape using consecutive sets of mated rolls, each of which makes only incremental changes in the form. The sum of these small changes in form is a complex profile.

Reasonable price, good attitude of consultation, finally we achieve a win-win situation,a happy cooperation!

-
High Quality Tile Making Machine - rain gutter...
-
oem Cold Roll Forming Machine factories - C Z ...
-
Chinese wholesale Steel Roll Forming Machinery ...
-
2019 High quality Cold Roll Forming Machine - ...
-
High Quality Door Frame Rolling Machine Supplie...
-
Wholesale Sandwich Panel Making Machine Supplie...